Sheet stamping
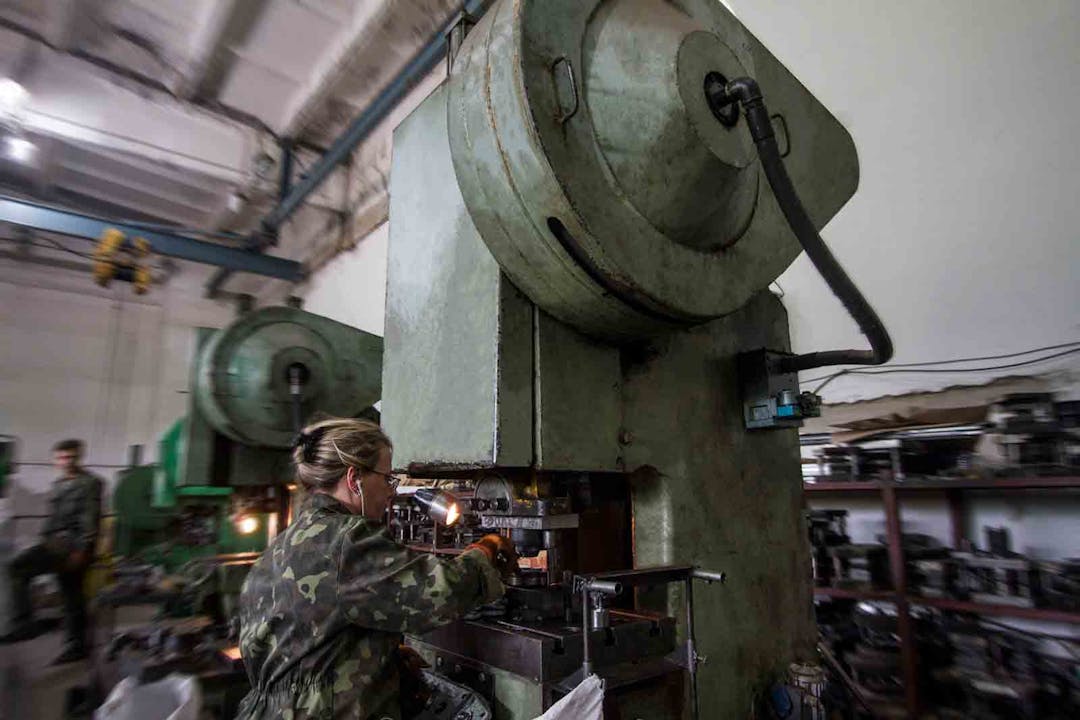
Promservice specializes in the production of stamped components. We offer a wide range of products for different applications, as well as sheet metal stamping services on your tooling.
For the production of stamped components, we use crankshaft pneumatic presses. They allow working with sheet material with a thickness of 0.15 to 5 mm. The maximum force when manufacturing a part is 100 t.
We have pneumatic presses with forces of 15, 25, 40, and 100 tons.
Sheet metal stamping - products for various applications
Sheet metal stamping is a manufacturing technology that allows forming metal parts from sheet materials such as steel, aluminum, brass, and copper. The process involves the use of blanking, bending, or combination dies to obtain the required shape and size of parts. Promservice company specializes in sheet metal stamping, offering customers the production of products of any complexity with high accuracy and quality of execution.
Main features of the technology
The production of stamped components is based on the use of special dies that can process metal sheets under pressure. This makes it possible not only to cut, but also to bend the metal, forming various structural elements from it. Modern technologies allow stamping to be performed at high speed and accuracy, which is critical for mass repair or production.
Due to the automation of the process, stamping is carried out with minimal material losses, which ensures high production efficiency. The use of various types of dies, such as blanking or bending, allows adapting the process to the specific needs of the customer, ensuring the receipt of products of various configurations and sizes, the cost of which is affordable for everyone.
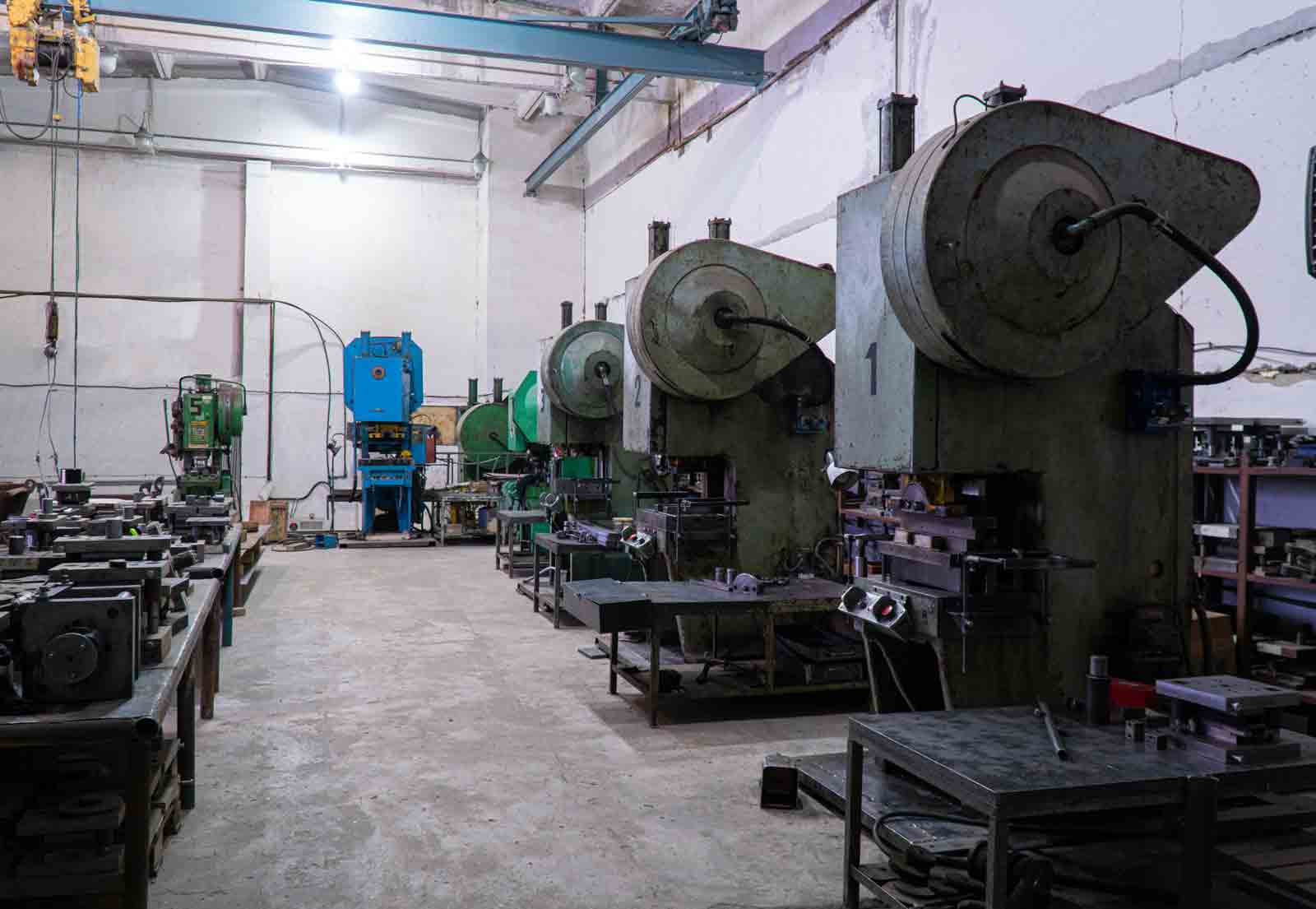
Types of stamping
Die cutting stamps
Die cutting stamps are used to cut out parts from sheet metal. They are used for the production of products such as brackets, clamps, nuts, and bolts.
Bending stamps
Bending stamps allow you to form sheet metal parts of a certain shape. They are used for the production of products such as grids, profiles, and pipes.
Combined action stamps
Combined action stamps combine the functions of blanking and bending. They allow you to cut out parts with slots or holes.
Stamped Component Production – Main Stages
The production of stamped components follows this sequence of actions:
Material Preparation
Selection of appropriate sheet metal (steel, aluminum, copper, etc.) and its preliminary processing to reduce internal stresses.
Blank Cutting
Cutting sheets into blanks of required sizes using laser or mechanical equipment.
Stamping
Cold sheet stamping process using specialized dies.
Cleaning and Grinding
Removal of burrs, oxide layers, and other defects from the surface that appear after stamping, to prepare the part for further production stages.
Quality Control
Checking the dimensions, strength, and compliance of parts with technical requirements, followed by marking, packaging, and shipping to the customer.
Materials
Steel
Steel is the most common material for stamping. It has high strength, rigidity, and wear resistance. Steel is used for the production of a wide range of parts, from simple brackets and nuts to complex car bodies and assemblies.
Brass and copper
Brass and copper have high plasticity and are easily stamped. They are used for the production of parts that must be resistant to corrosion and oxidation.
Aluminium
Aluminium is a lightweight and strong material that is well suited for stamping. It is used for the production of parts that must be lightweight yet strong.
Areas of application for stamped products
Sheet metal stamping is a highly efficient method of manufacturing metal parts, which is widely used in various industries. Due to its accuracy and cost-effectiveness, stamped components are indispensable in many areas.
Furniture production
Stamped components are used for the production of metal frames for chairs and tables, hinges for doors and drawers, guides for sliding mechanisms, as well as decorative elements such as handles and overlays.
Automotive industry
Sheet metal stamping is used for the manufacture of body panels, suspension parts, brake system elements, as well as various fasteners and brackets.
Construction and architecture
Stamped metal profiles are used for creating building frames, fasteners, cladding materials, and ventilation system elements.
Electrical engineering industry
Sheet metal stamping is necessary for creating cases for electrical appliances, contact plates, connectors, connecting elements, as well as parts for electrical panels.
Advantages of using sheet metal stamping
Sheet metal stamping services have a number of advantages that make their choice relevant for various industries:
High productivity
Stamping allows for the rapid production of a large number of identical parts, ensuring the efficiency of mass production
Reduced production costs
Optimization of material use and minimization of waste contribute to a reduction in the total production cost
Precision of parts
All stamped components have high geometric accuracy of products, which is critical for technically complex projects
Design flexibility
The technology allows for the implementation of a variety of design solutions, from simple to very complex shapes
Increased strength of products
The stamping process improves the mechanical properties of the metal, in particular its strength and resistance to deformation
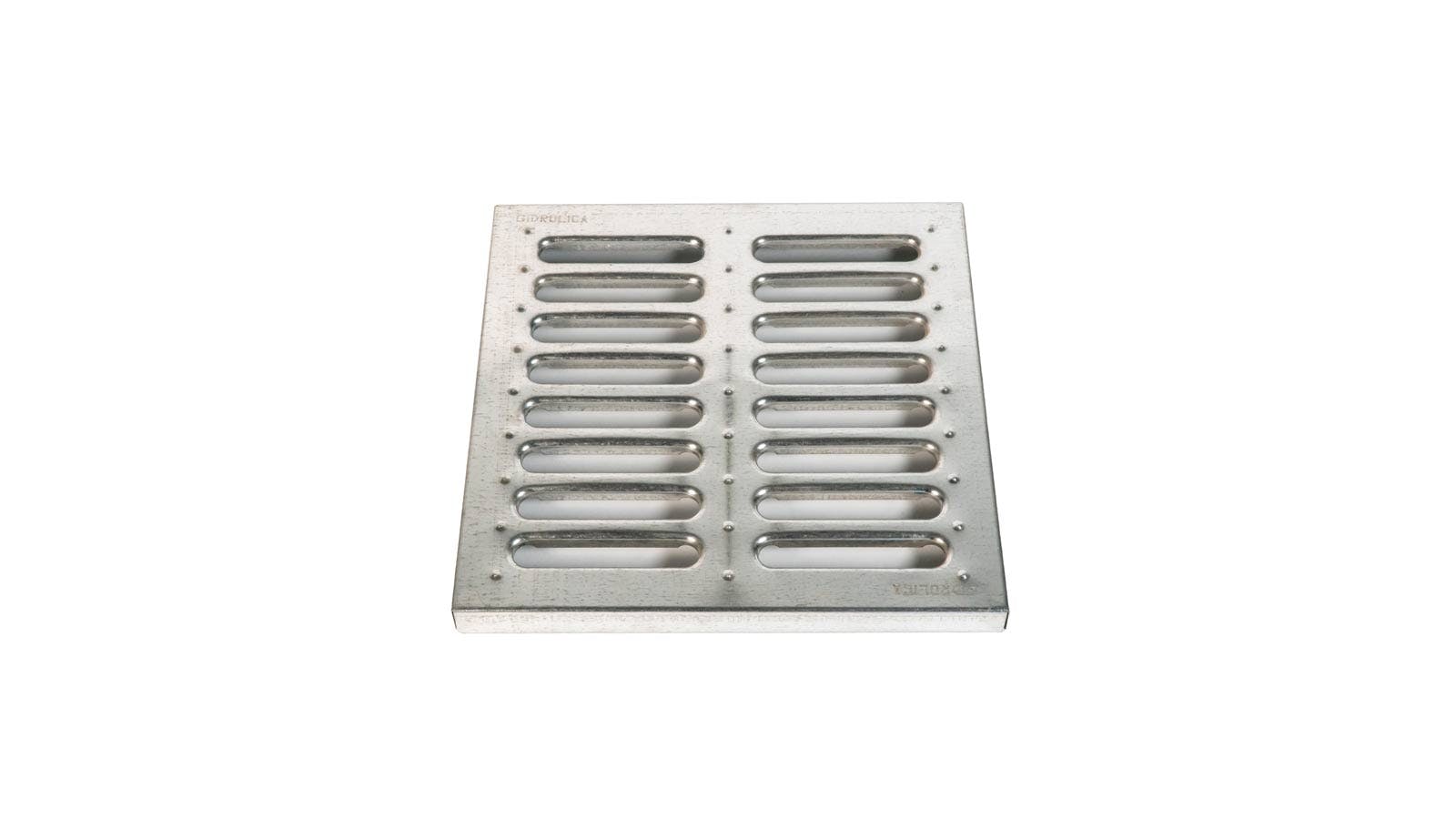
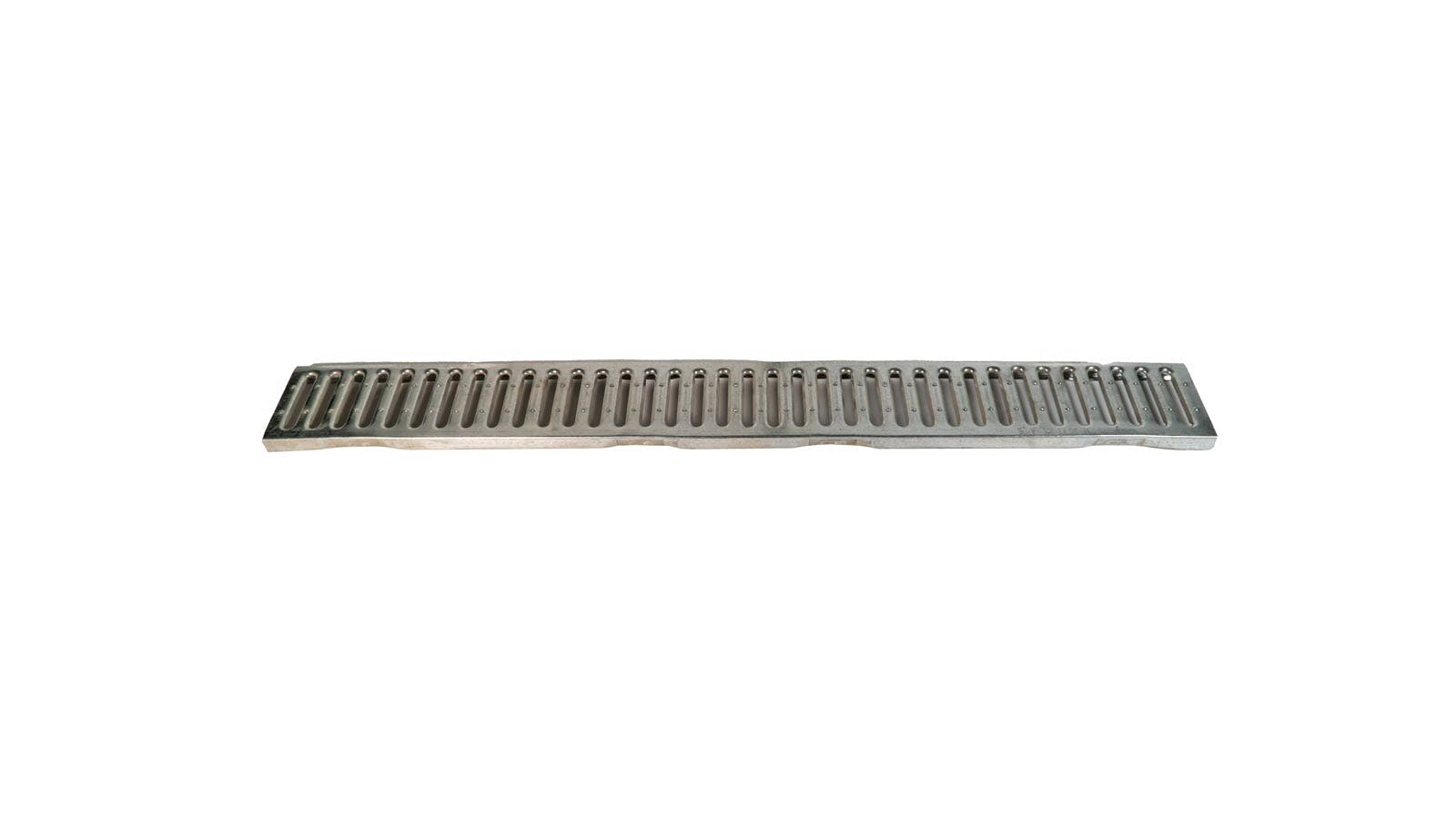
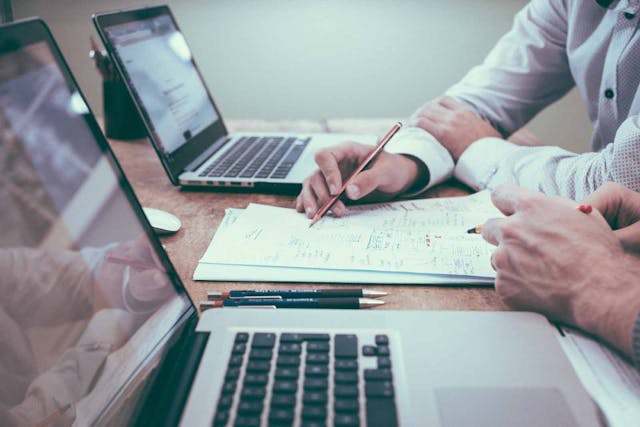